Transform Stock-Outs to “Stock-Ins” Before They Cause a Problem
Netstock is designed to identify potential stock-outs and transform crisis-style inventory management into inventory management excellence.For all businesses that need to provide high availability to keep their customers satisfied, stock-outs are quite simply a nightmare. Dealing with angry customers can send the stress levels of your employees soaring. Your order and sales staff will do whatever they can to placate the customer, while your purchasing and planning colleagues have to run in circles, begging and pleading with suppliers or manufacturing. Whichever way you look at it, it’s not a pretty picture.
Unfortunately, as much as it would be wonderful to banish the stock-out completely, they are a reality. And it is not necessarily faulty replenishment that is to blame. Predictions for supply and demand will never be completely perfect; the greater the inaccuracy, the greater the risk of stocking out.
How to deal with stock-outs
Perhaps the approach to dealing with stock-outs should be shifted to focus on items that are stocked out prior to the request for the item. Netstock monitors inventory KPIs and quickly identifies current and potential stock-out risks based on their value to your business. The call to action for each item is as follows:
Check that the stock-out is legitimate – misleading data can distort the picture, and you don’t want to put a plan of action in place based on inaccurate data. Double-check the current stock level, and then factor in supplier orders and purchase orders.
Before making plans to find stock, ascertain whether your customer will wait for the stock and for how long. Good communication could save the day!
If remedying the stock-out immediately is the only option, determine what can be done. Is there an opportunity to expedite an existing purchase order or to transfer stock from a nearby location? You may want to consider air-freighting a portion of the order. Can you source from an alternate supplier or even a competitor? This might seem extreme, but it may be worth the effort and expense if you can prevent the loss of a sale or a customer.
Most importantly, resolve why the stock-out occurred and avoid repeating the same set of circumstances. Constantly working to resolve the root causes has proven to reduce the occurrence of stock-outs over time.
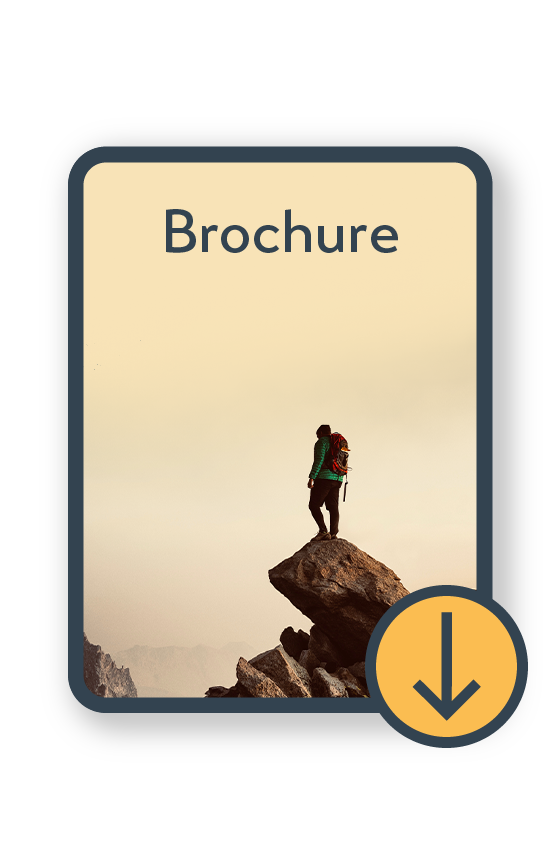
5 benefits of insight driven inventory management Brochure
Download PDFDiscover strategies to maximise warehouse productivity
Achieving optimal warehouse efficiency in a period of market decline is paramount; any inefficiency directly impacts your customers and bottom line. Taking the steps to maximise productivity now will position your company for success when the market improves. Smarter logistics and WMS solutions are the key to client satisfaction. Ensure you get your products to your clients on time and in full.
Watch the webinar recording to discover the strategies and processes to reduce errors, maximise productivity, and increase operational efficiency.
If you need any more information on, Inventory Management Software, stock-outs or NETSTOCK, contact us here 1300 857 464 (AU) or 0800 436 774 (NZ), or send an email to sales@kilimanjaro-consulting.com.