When and Why Your Business Should Consider a Warehouse Management System (WMS)
Achieve a paperless warehouse and total control of your inventory with a Warehouse Management System.The processes in your warehouse play a crucial role in ensuring smooth operations and customer satisfaction. Attaining peak efficiency is essential; any inefficiencies can have significant consequences for your customers and bottom line. Relying on manual, paper-based processes creates bottlenecks that are difficult to overcome. Your MYOB ERP system, together with a Warehouse Management System (WMS) can truly take your operational efficiency to the next level.,
What is a Warehouse Management System?
A WMS streamlines operations by automating various tasks within the warehouse, including inventory tracking, picking, order fulfilment, and shipping. A WMS enables organisations to make informed decisions, reduce manual errors, improve inventory accuracy, and enhance warehouse efficiency. It provides real-time visibility into inventory levels and the movement of goods.
Six Signs That Your Business is Ready for a WMS
These 6 signs indicate your business might be ready for the transformative step of implementing a Warehouse Management System.
1. Inaccurate Inventory Levels
Disparities between recorded inventory levels and actual stock can present multiple challenges for organisations. Stockouts result in lost sales and dissatisfied customers who may turn to competitors. Conversely, overstocking ties up your capital in the warehouse, limiting your ability to adapt to market changes and increasing holding costs. A WMS that offers real-time inventory tracking and bin management will elevate your inventory management capabilities.
2. Hidden inventory in your warehouse
While inventory management products track the overall stock level and prompt restocking, when necessary, they may fall short in pinpointing the exact location of each item within the warehouse. Bin and location management is a crucial feature of a WMS. It can provide a precise location of all stock within a warehouse, down to specific aisles or bays and even multiple locations within one warehouse. The combination of real-time inventory tracking and bin management allows your organisation to quickly locate products within your warehouse, helping you maintain optimal stock levels, reduce carrying costs, prevent stockouts or overstocks and ensure smoother operations.
3. Growing Inventory and Order Complexity
As your business expands, you might experience a surge in inventory volume and order complexity. Complex orders with bulk prices, customisations, and backorders demand meticulous coordination to ensure prompt fulfilment and minimise errors. Manual, paper-based systems struggle to handle these complexities effectively, leading to delays, errors, and dissatisfied customers. Implementing a WMS will streamline these processes by automating tasks and enabling you to manage larger inventories and more intricate orders efficiently.
4. Inefficient Use of Warehouse Space
Poorly optimised warehouse space can lead to difficulty finding stock, wasted time when picking, and lower return on your space investment. These additional expenses can escalate to rent, maintenance, and labour and reduce overall profitability. A WMS has intelligent slotting capabilities that ensures efficient use of warehouse space. This makes items easier to find, reducing the picking and packing route and ensuring faster order fulfilment.
5. High Operational Costs
Rising labour or overtime expenses can indicate that your current processes are inefficient. This issue leads to lower profit margins, making it harder to invest, expand, or stay competitive. Adopting a WMS will automate and streamline various processes, such as order processing and carton packing, enabling your organisation to adopt a smarter picking strategy.
With the WMS in place, you will benefit from real-time inventory visibility and task prioritisation. This empowers your workforce to focus on critical tasks, leading to quicker order fulfilment. Moreover, efficient replenishment ensures that pickers always have sufficient stock, minimising downtime and boosting overall productivity.
With the implementation of a WMS, the dependence on manual processes will decrease, leading to a notable reduction in overtime work and a lowering of operational costs for your organisation.
6. Difficulty Meeting Compliance Standards
Customers expect live, real-time traceability for their orders. Meeting compliance standards or achieving product traceability is incredibly challenging when relying on out-of-date processes or tools. A WMS not only manages product movements within the warehouse but also serves as a comprehensive data repository. The WMS keeps meticulous records of every transaction and movement throughout the shipping and supply chain, providing a full audit trail. Have complete visibility into the journey of your products from origin to the end consumer.
Key opportunities to transitioning to a WMS
Moving from a paper-based system to a WMS brings more than just operational efficiencies.
Gain Industry-Specific Guidance
Leverage the wealth of experience possessed by WMS providers to improve your warehouse efficiency. Their industry-specific expertise allows them to offer tailored advice for your warehouse operations. They draw insights from successful practices in similar companies while helping you avoid potential pitfalls.
Conduct an Operational Analysis
Deep dive into your existing processes to thoroughly analyse your operations, identify essential tasks, and highlight functions that could benefit from refinement. This reflective process lends a new perspective to your warehouse operations, identifying opportunities for improvement that can be implemented alongside the new system. Get ahead of demand planning trends to improve efficiency and customer satisfaction.
Design Optimised Workflows
The transition to a WMS creates a unique opportunity to redesign and improve upon your existing workflows to improve overall efficiency. This process allows you to carefully evaluate each operation within your warehouse, determining how it fits into your overall company process and reviewing processes for maximum efficiency.
The Benefits of a WMS
Implementing a WMS offers numerous benefits, including:
- Providing real-time visibility into your inventory, enhancing accuracy and control.
- Automating manual processes, increasing efficiency, and reducing errors.
- Optimising warehouse space usage, leading to faster, more efficient order fulfilment.
- Enhancing traceability and compliance with regulatory standards.
Transitioning from a paper-based system to a Warehouse Management System is a significant move that can enhance your operations and provide a platform for growth. Integrating a WMS like eveXso with MYOB Advanced or MYOB Exo, not only addresses existing challenges but also offers opportunities for continuous improvement. If you are experiencing any of the highlighted issues, moving to a WMS might just be the strategic step-change your business needs.
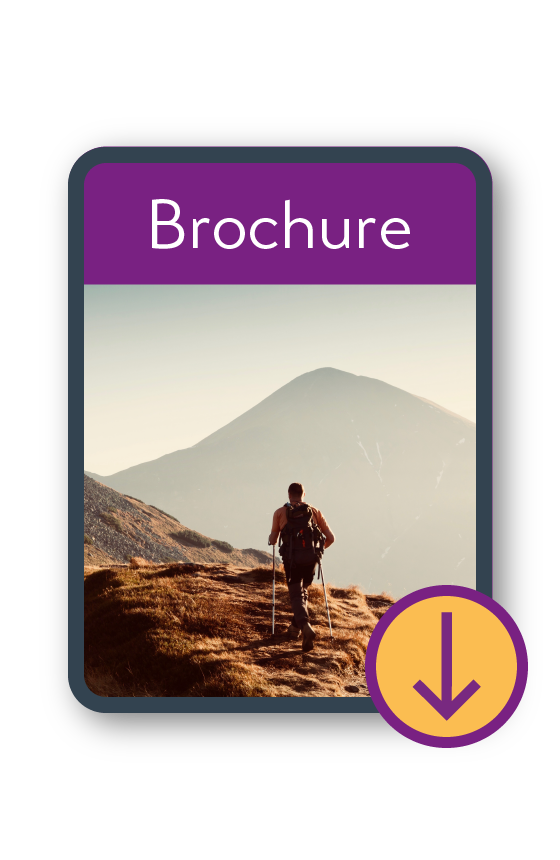
eveXso Brochure
Download nowBuild a smarter warehouse for better results
With customers expecting fast and accurate shipping, any bottleneck in your warehouse operations can lead to frustrating delays, disappointed customers, and reduced long-term revenue. Join our free webinar and discover how to build a smarter warehouse and improve customer satisfaction.
Discover strategies to maximise warehouse productivity
Achieving optimal warehouse efficiency in a period of market decline is paramount; any inefficiency directly impacts your customers and bottom line. Taking the steps to maximise productivity now will position your company for success when the market improves.
Watch the webinar recording to discover the strategies and processes to reduce errors, maximise productivity, and increase operational efficiency.
Kilimanjaro Consulting is the premier implementing partner of MYOB Advanced and MYOB Exo across Australia and New Zealand. We are experts at integrating third-party warehouse management solutions into your MYOB ERP to improve efficiency. To start a conversation about how to improve your warehouse management process, email samacs@kilimanjaro-consulting.com, or call 1300 857 464 (AU) or 0800 436 774 (NZ).