Can your system handle your complex inventory requirements?
Improve your inventory control and accuracy with MYOB inventory management solutions.Poor inventory management can lead to stockouts, overstocking, and significant financial losses. As your organisation continues to grow and become increasingly complex, there are inventory metrics and costs that you should be tracking, in addition to carefully balancing your stock levels.
Understanding complex inventory requirements
Simple inventory-based businesses handle small product ranges, standard pricing, single locations, and few suppliers. On the other hand, complex operations may include:
- Quantities of SKUs (Stock Keeping Units) in the thousands,
- Multiple warehouses or retail locations,
- Complex pricing structures based on specific customers,
- Many different suppliers, some of which provide the same SKUs with different cost prices and lead times,
- Much larger distribution requirements including teams to pick, pack, and send out orders,
- More stringent supply chain management and oversight,
- International import and export compliance, including the ability to transact in multiple currencies.
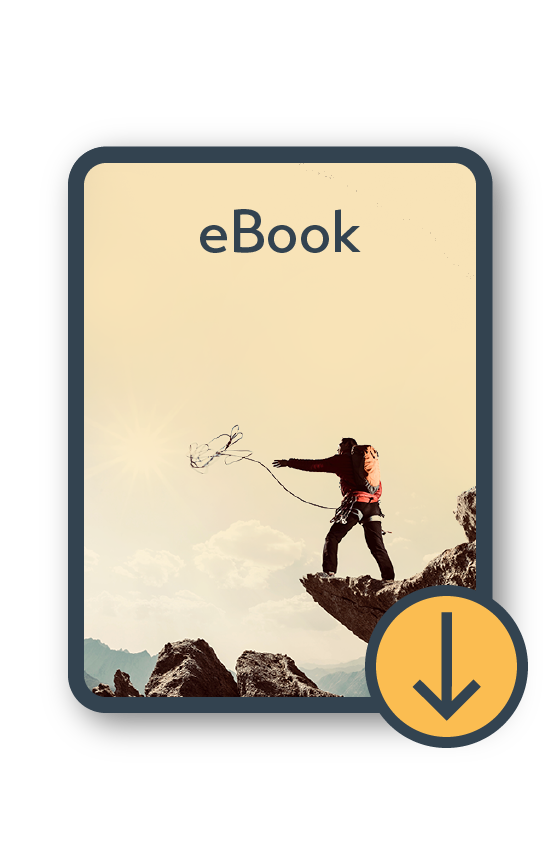
Defining the challenges to a wholesale business eBook
Download nowChallenges of managing complex inventories
As a result of these complex requirements, many growing organisations face challenges with inventory management:
- Managing a diverse product range, especially regarding storage requirements, handling processes, seasonal fluctuations, or managing obsolete lines,
- Having real-time visibility across multiple warehouses or even multiple locations within one warehouse,
- Accurately predicting demand for a growing list of products is fraught with risk,
- Coordinating with suppliers and distributors to receive and distribute goods efficiently,
- Maintaining compliance for perishable or pharmaceutical products,
- Accurately tracking costs, potentially across multiple delivery sites, in multiple currencies, and with dynamic lead times,
- Shipping container volumes to optimise ordering from overseas suppliers,
Strategies to improve inventory control and accuracy
Take control of stock control by focusing on forecasting and visibility. Automate error-prone processes wherever possible to manage the risks of human input and improve overall efficiency. Implementing RFID or barcode scanning ensures accuracy in your warehouse, eliminating confusion of what is being sold or packed for an order. When you know exactly what you have sold and have in stock, you can more easily and accurately forecast for the future. Optimising your warehouse layout to streamline picking and packing can also make your team more efficient.
Building strong relationships with suppliers can lead to better pricing as well as market insights into what they sell to other customers. This can be invaluable in both boosting profit and staying up to date with market requirements. Suppliers want you to have the right inventory on hand so that you can sell more and replenish in time. The right system can aid and assist in planning inventory levels and refills to ensure they arrive in a timely manner without adding to the risk of overstocking.
MYOB Exo inventory management solution
MYOB Exo is a sophisticated ERP system that can fully integrate your financial and business management data. The software has been deployed in over 3000 mid-tier organisations across Australia and New Zealand, and they have benefitted from the typically lower cost to implement compared to other mid-market ERP packages.
Inventory based companies naturally gravitate towards MYOB Exo due to its robust stock control and customisability, as well as the deep integration between the Inventory and Finance modules. However, when your business continues to grow you may need additional functionality to help manage your increasingly complex inventory requirements.
Tracking costs per location
When you have warehouses in different locations, it affects the cost of your inventory and the profit you can make. Whether you are paying different rent or different shipping rates per location, this all affects your bottom line. MYOB Exo software does not cater for different costs per location.
Different cost of goods tracking models
First in First Out (FIFO), stock tracking is very important for certain businesses, for example, those with perishable inventory. FIFO assumes that the first stock bought in is the first stock sold out. FIFO tracking then assigns the oldest inventory costs to the most recent sales. Tracking stock movement in this way gives a more accurate picture of your business’s profitability. Likewise, some businesses prefer to use the Last in First Out (LIFO) model especially during times of inflation to avoid overstating profits, reduce the impact of tax, and improve cash flow.
MYOB Exo uses an average measure for COG/S (cost of goods/cost of goods sold). It is a simple metric, however, you cannot see the clearest picture of your business like you can when using other tracking models.
Bin-management
A typical warehouse may have multiple bins per stock item, to optimise picking efficiency and to control stock levels. But managing so many small units within your warehouse can be a challenge for many ERP systems. Track MYOB inventory across multiple warehouses and locations, however multiple bin locations within the same warehouse is out of the scope of its functionality.
Clever software solutions to support inventory operations
There are a variety of alternative systems available to help you manage your organisations complex MYOB inventory requirements. These take the form of cloud-based ERP software with improved functionality as well as add on products integrated with MYOB Exo to improve efficiency.
MYOB Acumatica
MYOB Acumatica (formerly MYOB Advanced) is a powerful cloud-based business management system with dedicated inventory management functionality. It is based on the fastest-growing cloud ERP platform in the world, Acumatica, and localised for the Australian and New Zealand requirements.
MYOB Acumatica has the capability, features, and automations to make inventory management easier and more accurate for your team:
- Maintain detailed information on your inventory including supplier codes, barcodes, cost and sell pricing history,
- Track inventory levels and costs across multiple warehouses and locations,
- Advanced MYOB inventory management features include serial and batch tracking, kit assemblies, and bin location with pick priorities,
- Manage multiple customer and supplier price lists including order discounting policies,
- Multiple stock valuation methods including FIFO and LIFO tracking,
- Integrated workflows to streamline the order-to-despatch process including automated updates and notifications, purchase order approvals,
eveXso
eveXso is a Warehouse Management Solution (WMS) designed to improve your service levels and efficiency across your warehouse. It streamlines order picking and packing, bin management, and receipting of goods. eveXso also gives management anytime, anywhere visibility to track and resolve issues.
If you need detailed bin management, then eveXso can supplement MYOB Exo to give you accurate picking, packing and shipping functionality at a bin level. eveXso is cloud-based and usable via mobile app, so you can access up to date, real-time distribution information from any location in the warehouse. eveXso seamlessly integrates with both MYOB Acumatica and MYOB Exo.
Netstock
Netstock is an inventory management and demand planning solution designed to give you detailed information of all stock, across your entire organisation. By leveraging historical sales and purchasing information, including lead times, Netstock will calculate optimised stock levels for all groups of products. It guides you to place the correct orders at the right time with easy-to-use dashboards, KPIs, and forecasts.
Using Netstock in conjunction with MYOB Exo can give you the detailed information you need to make good inventory decisions. Netstock also integrates directly into MYOB Exo and MYOB Acumatica, so you don’t have to re-key your Purchase Orders into your ERP system.
Taking the next steps
You MYOB Exo system is a powerful tool, although like any available solution it has its limitations. You can extend the functionality your system by implementing add-on solutions like Netstock or eveXso. These systems improve particular areas of your business as well as moving you along the pathway to the cloud.
Carefully weigh the benefits and challenges of implementing a cloud ERP. There might be other positives in moving to the cloud, like eliminating costly on-premise server maintenance. MYOB Acumatica is a powerful tool for those organisations ready to take the next steps. Ensure you are informed about the implementation process and the other areas you can see efficiency improvements. MYOB Acumatica is also compatible with both Netstock and eveXso. If you choose to move your ERP system to the cloud at a later date, these integrations can be preserved to streamline the transition.
How can software solutions improve real businesses?
The Arcadia Corporation successfully transitioned into the cloud and achieved a single, efficient platform from which they now manage their Inventory, Accounts, and CRM. They decided to move to MYOB Acumatica when they opened a new location and needed extra support managing their inventory complexities. Moving from MYOB Exo to MYOB Acumatica improved functionality and provided end-to-end management of its products. Additionally, integrations with their core business management system enhanced visibility and simplified reporting for the finance and sales teams.
Learn more about the real benefits of moving your organisation into the cloud by reading the case study here.
Our team is ready to help solve your complex inventory needs. To learn more about MYOB Acumatica, EveXso, Netstock or other MYOB inventory management tools, please contact our team via email at migrations@kilimanjaro-consulting.com or call 1300 857 464 (AU) or 0800 436 774 (NZ) to book a free demonstration.